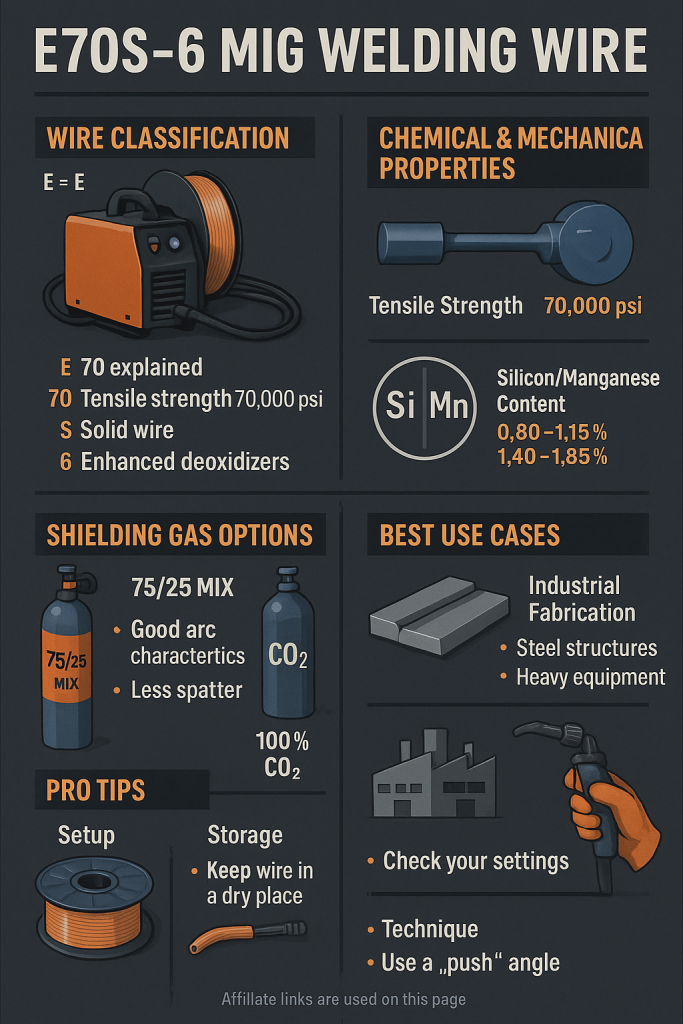
When it comes to MIG welding mild steel, E70S-6 welding wire is a go-to filler metal used across industries—from structural steelwork to automotive fabrication. It’s known for its excellent arc stability, high deposition rate, and strong mechanical properties.
Whether you’re a welder, fabricator, or welding engineer, understanding E70S-6 is critical for making informed decisions about joint strength, weld quality, and process efficiency. In this guide, we break down everything you need to know about this essential wire type.
Types, Classifications, and Variants
E70S-6 is part of the AWS A5.18 classification system for solid carbon steel electrodes and rods used in gas metal arc welding (GMAW). Here’s what the designation means:
- E – Electrode
- 70 – Minimum tensile strength of 70,000 psi
- S – Solid wire
- 6 – Indicates the wire’s chemical composition and performance characteristics
Comparison with Other Carbon Steel MIG Wires:
- E70S-3
- Lower deoxidizer content
- Less tolerant of mill scale or rust
- Cleaner base metals are required
- E70S-6
- Higher levels of silicon and manganese
- Designed for welding over mill scale, light rust, or surface contamination
- More fluid weld puddle for flatter beads
- E70C-6M (metal-cored)
- Similar chemical composition to E70S-6
- Offers higher deposition rates
- Requires more expensive equipment and optimized parameters
Key Characteristics & Properties
E70S-6 wire stands out for its versatility and weld quality on less-than-perfect base metals. Let’s take a closer look at its technical properties:
- Tensile Strength: 70,000 psi (minimum)
- Yield Strength: ~58,000 psi
- Elongation: ~22% in 2 inches
- Recommended Shielding Gas:
- 75/25 Argon/CO₂ for cleaner, more controlled arcs
- 100% CO₂ for deeper penetration and cost-effectiveness
- Silicon Content: 0.80–1.15%
- Manganese Content: 1.40–1.85%
- Diameter Availability: .023″, .030″, .035″, .045″, and larger for industrial applications
Real-World Example:
If you’re welding mild steel tubing for handrails or machinery guards with surface mill scale, E70S-6 will give you a smooth, low-spatter weld bead that requires minimal cleanup.
Process Considerations
Compatibility with Welding Processes
- ✅ GMAW (MIG Welding) – Primary application
- ❌ Not suitable for FCAW, GTAW, or SMAW
Equipment Notes:
- Compatible with both transformer and inverter-based MIG machines
- Works well in spray, short-circuit, and globular transfer modes
- Ideal for semi-automatic or robotic applications
Pros:
- High feedability in wire feeders
- Excellent bead appearance
- Tolerant to minor surface contaminants
Cons:
- Not designed for high-alloy or exotic metals
- Less effective on dirty or heavily rusted steel than flux-core options
- Needs shielding gas—can’t be used outdoors without wind protection
Application Use Cases
E70S-6 is a workhorse wire used in general fabrication and manufacturing:
Common Industries:
- Structural steel erection
- Heavy equipment repair
- Shipbuilding
- Automotive and trailer frame welding
- Agricultural implement manufacturing
Compatible Metals:
- A36 mild steel
- Hot-rolled steel
- Low-carbon structural plates and tubing
Ideal Conditions:
- When high productivity, flat bead profiles, and minimal post-weld cleanup are important
- When working with slightly rusty or mill-scaled materials
Best Practices & Pro Tips
Here’s what experienced welders need to keep in mind:
- Use the Right Gas Mix:
75/25 Argon/CO₂ delivers cleaner welds; 100% CO₂ increases penetration but increases spatter. - Clean Just Enough:
Though E70S-6 handles light contamination, don’t push it—heavy rust or paint can still cause porosity. - Dial in the Voltage and Wire Speed:
Start with manufacturer specs and fine-tune based on sound and bead shape. A smooth “buzz” sound = optimal settings. - Avoid Excess Heat Input:
Especially when welding thinner material. Use pulsed MIG or short-circuit transfer to avoid burn-through. - Watch for Silicon Islands:
After welding, shiny silicon deposits may form in the weld toe area. These should be ground off before painting or coating. - Store Wire Properly:
E70S-6 is prone to rust if stored in humid conditions. Keep it in sealed containers or use wire feeders with covers.
Conclusion
E70S-6 MIG welding wire is the top choice for fabricators and welders dealing with carbon steels that aren’t in pristine condition. Its chemical makeup allows for smooth arcs, flat welds, and strong joints even when base metals have minor mill scale or rust.
If you’re looking to balance performance, affordability, and ease of use, this wire is probably the right fit for most carbon steel welding jobs.
Note: Some links on this page may be affiliate links. If you click and purchase, we may earn a commission at no extra cost to you. We only recommend products we use and trust.
Leave a Reply