MIG welding is known for its speed and ease, but it isn’t immune to issues, especially porosity. If you’ve ever laid a bead that looked more like Swiss cheese than solid metal, you’re not alone. Porosity is one of the most common (and frustrating) MIG welding problems, but the good news is: it’s solvable. This quick guide covers the causes and actionable fixes to help you get back to laying clean, reliable welds.
What Is Porosity in MIG Welding?
Porosity happens when gas gets trapped in the molten weld pool and forms bubbles as the metal solidifies. These gas pockets can severely weaken your weld, cause leaks in pressure vessels, and ruin the appearance. There are two types:
- Surface porosity: visible holes on the weld face.
- Subsurface porosity: hidden defects inside the weld, often only found with X-ray or ultrasonic inspection.
Both types are bad news, but they’re usually preventable.
Common Causes and Fixes
1. Contaminated Base Metal
Problem: Dirt, rust, oil, paint, or moisture on the workpiece can create gas when burned, leading to porosity.
Fix: Clean the metal thoroughly with a wire brush, grinder, or acetone before welding. Even new steel can have mill scale or oil that needs removal. See the clean side on the right.
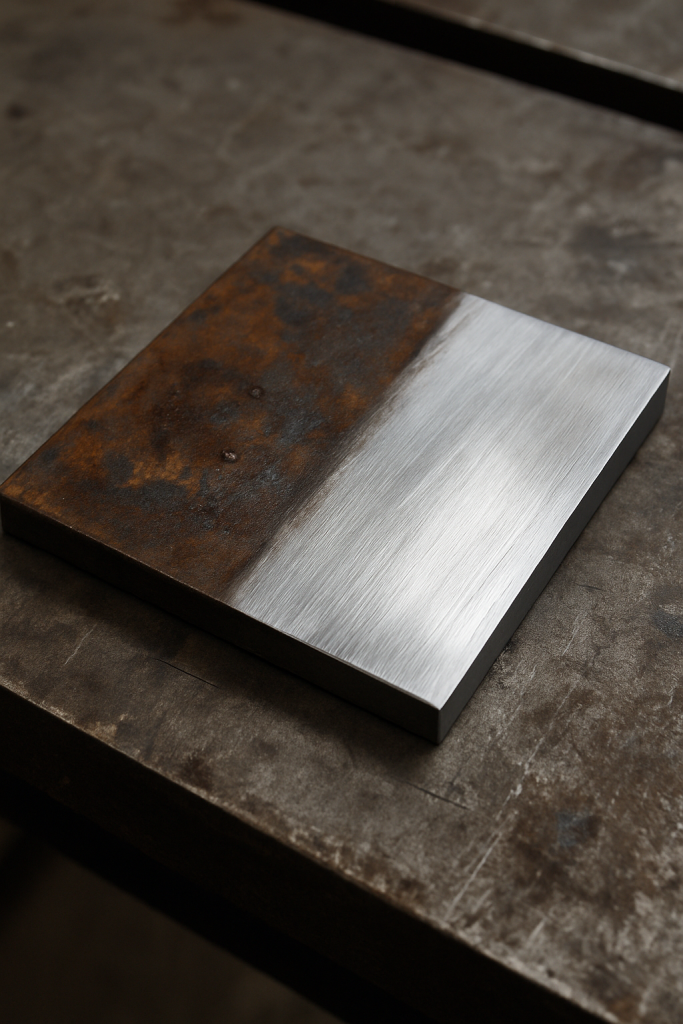
2. Poor Shielding Gas Coverage
Problem: If your gas isn’t fully protecting the weld, air can mix in and cause bubbles.
Fixes:
- Check your flow rate: For most MIG setups, 20–30 CFH is ideal. Too low or too high can cause turbulence.
- Inspect for leaks: Look for cracks in hoses or loose fittings.
- Avoid wind: Even a slight breeze can disrupt shielding gas. Weld indoors or use wind guards when possible.
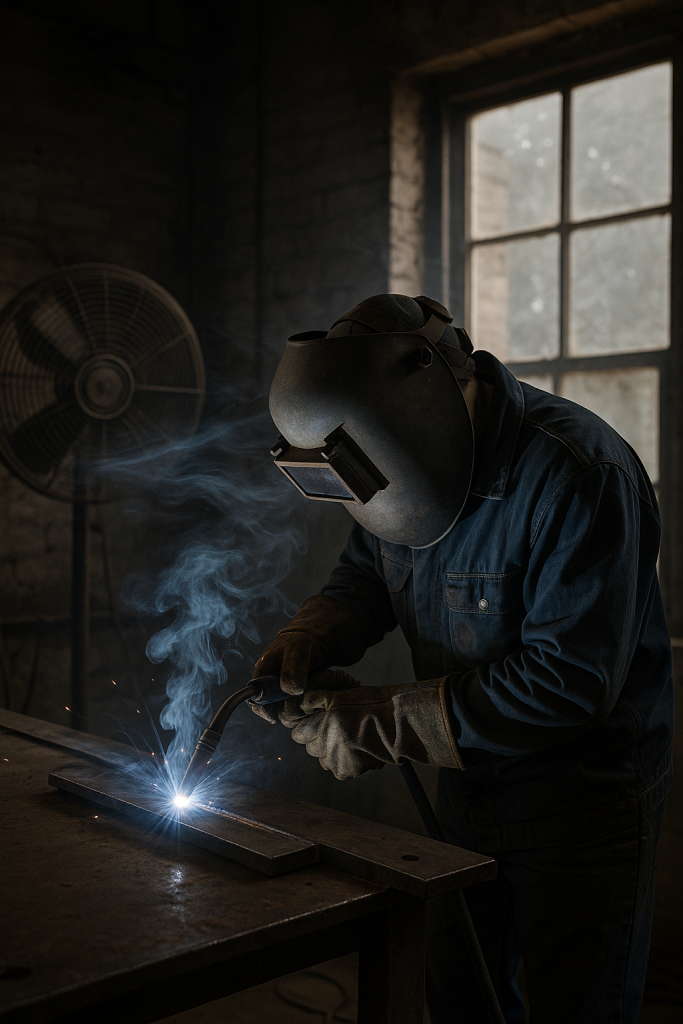
3. Incorrect Stick-Out (Electrode Extension)
Problem: If your wire stick-out is too long, it reduces gas shielding and increases spatter.
Fix: Keep stick-out around 3/8″ to 1/2″ for solid MIG wire. Flux-core may allow for a bit more, but always refer to the manufacturer’s specs.
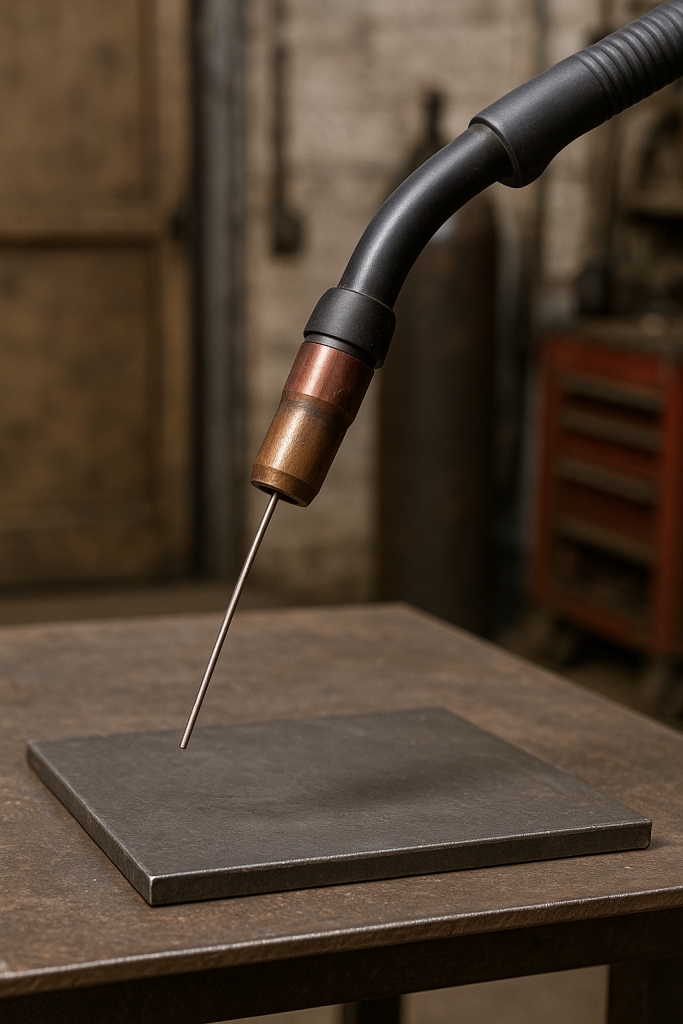
4. Wrong Gun Angle or Distance
Problem: Angling the gun too much or holding it too far away from the workpiece can compromise gas coverage.
Fix: Use a push technique with the gun held at a 10–15° angle from vertical. Keep the nozzle about 3/4″ from the puddle.
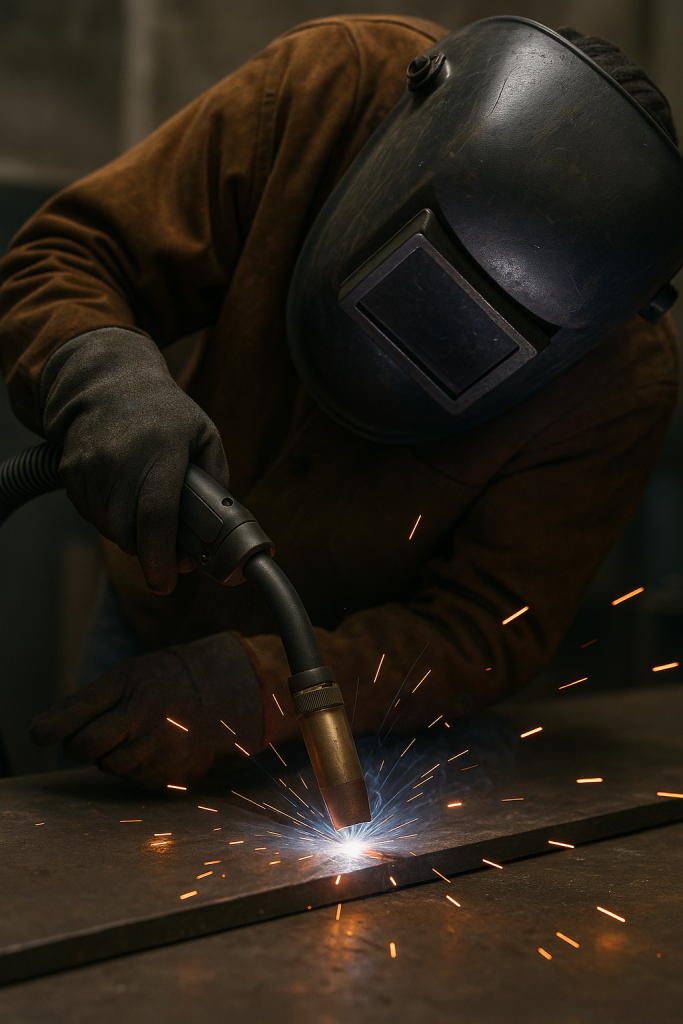
5. Dirty or Damaged Consumables
Problem: Spatter buildup inside your nozzle or a bad diffuser can affect gas flow.
Fix: Regularly clean or replace the nozzle, tip, and diffuser. Use anti-spatter spray to prevent buildup.
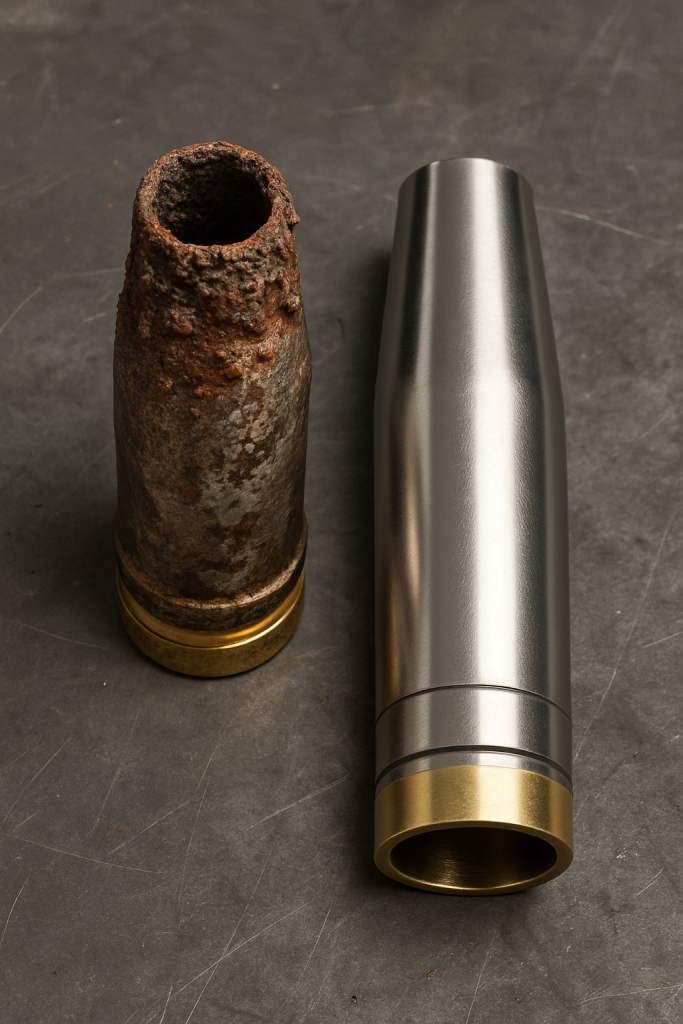
6. Wrong Wire or Gas Combo
Problem: Using the wrong type of wire or gas for the job can cause an unstable arc and porosity.
Fix: Make sure you’re using the right filler wire for your material. For mild steel, ER70S-6 with 75/25 argon/CO₂ is the common go-to. Stainless or aluminum will require different combinations.
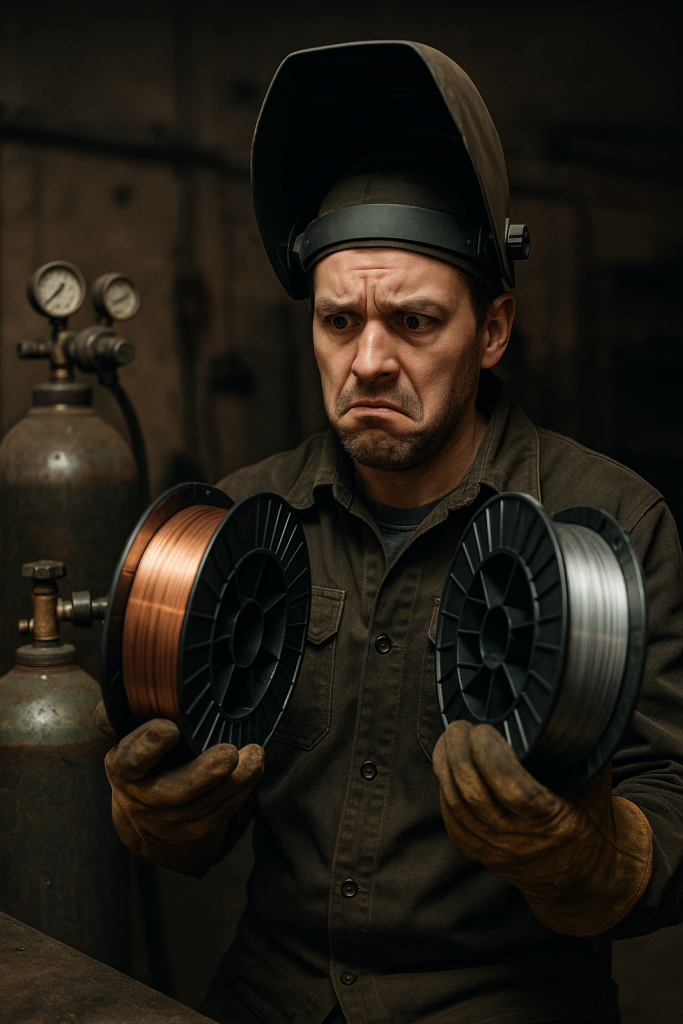
Pro Tip: Keep a Checklist
If you’re running into porosity issues often, build a pre-weld checklist. Here’s a simple one:
- Clean the metal
- Check gas flow and hose integrity
- Inspect consumables
- Confirm correct wire/gas combo
- Set gun angle and stick-out properly
Final Thoughts
Porosity in MIG welds can be frustrating, but it’s rarely random. Usually, it comes down to gas coverage, cleanliness, or technique. By understanding the root causes and dialing in your setup, you’ll be able to produce clean, professional-quality welds every time.
This post may contain affiliate links. We may earn a commission if you purchase through them—at no additional cost to you. We only recommend products we trust for quality and performance in the shop.
Leave a Reply