The Science of Welding: MIG, TIG, and Stick Compared – Plus the Real Cost Per Foot of Weld
Introduction
In the world of metal fabrication, welding is both art and a science. Understanding not just how to weld but why certain processes work better—and cost less—in specific scenarios is essential for:
- Welders are optimizing efficiency in the booth.
- Engineers and designers make process-specific decisions during material selection.
- Fabrication buyers and project managers estimate costs accurately and competitively.
From the molecular thermodynamics of arc formation to the economic reality of consumables, each welding process—MIG (GMAW), TIG (GTAW), and Stick (SMAW)—brings trade-offs that can dramatically affect weld quality and cost per foot.
In this guide, we’ll break down:
- The science behind MIG, TIG, and Stick welding.
- How variables like speed, consumable use, and labor affect cost per linear foot.
- Real-world cost breakdowns and comparisons—to help you make informed decisions and reduce waste.
The Science of Welding Processes
MIG Welding (GMAW) – High Speed, Low Cost
Science Behind the Process:
- Arc Formation: A continuous solid wire is fed through a MIG gun, producing an electric arc between the wire and base metal.
- Shielding Gas: Typically a mix of argon and CO₂ to protect the weld zone from atmospheric contamination.
- Filler Metal Transfer: Spray or short-circuit transfer, depending on settings and thickness.
Molecular Level Insight:
- The arc melts both the electrode and base metal, fusing them at a localized point as electrons bombard the joint.
- Shielding gas prevents oxygen and nitrogen from contaminating the weld pool, which is crucial for metallurgy.
Strengths:
- High deposition rate and travel speed.
- Easy to learn and automate.
- Ideal for production shops and thin to mid-thickness steel.
Weaknesses:
- Requires shielding gas, limiting portability.
- Less suitable for windy outdoor environments or dirty/oxidized metal.
TIG Welding (GTAW) – Precision and Cleanliness
Science Behind the Process:
- Non-Consumable Tungsten Electrode creates the arc without melting itself.
- Filler rod is added manually (or autogenously).
- Shielded with pure argon (and sometimes helium blends).
Precision Metallurgy:
- Arc is extremely focused—ideal for very thin materials and dissimilar metals.
- Allows precise control of heat input, reducing heat-affected zones (HAZ) and distortion.
Strengths:
- Produces the highest quality and cleanest welds.
- Ideal for aluminum, stainless steel, nickel alloys, and precision aerospace components.
Weaknesses:
- Slowest process—low deposition rate.
- Skill-intensive; long arc-on time per weld.
- Highest cost per foot.
Stick Welding (SMAW) – Versatility and Ruggedness
Science Behind the Process:
- Uses a flux-coated consumable electrode.
- An arc is created between the electrode tip and the base metal.
- Flux burns off to create shielding gas and leaves a protective slag layer.
Molecular Dynamics:
- Flux deoxidizes and scavenges impurities in the weld pool.
- Slag forms a protective crust, improves cooling rates, and must be chipped away after the weld.
Strengths:
- Works in windy/outdoor settings without shielding gas.
- Lower upfront equipment costs.
- Suitable for structural steel, piping, and field repairs.
Weaknesses:
- Slower than MIG, more cleanup.
- Stub loss and slag introduce waste.
- Arc-on time is lower than GMAW.
Welding Variables That Impact Cost
To get to the real cost per foot, consider these key variables:
Variable | MIG (GMAW) | TIG (GTAW) | Stick (SMAW) |
---|---|---|---|
Travel Speed | Fast | Slow | Medium |
Deposition Rate | High | Low | Medium |
Consumable Efficiency | High (~90–95%) | Moderate (~75%) | Lower (~60% with stub loss) |
Power Usage | Moderate | High | Moderate |
Labor Skill Level | Moderate | High | Moderate |
Cleanup/Rework | Minimal | Minimal | Significant (slag chipping) |
Cost Breakdown Per Foot of Weld
Let’s compute the average cost per linear foot using common practices, consumables, and hourly wage estimates.
Assumptions:
- Labor rate: $40/hour
- Electricity: $0.12/kWh
- Mild steel or stainless steel applications
- Weld size: 1/4” fillet weld, 12” long
MIG Welding Cost Example
Consumable & Indirect Costs:
Item | Cost Estimate |
---|---|
Wire (ER70S-6) | $2.50/lb; ~0.035 lb/ft = $0.09 |
Shielding gas | $1.00/CFH; ~35 CFH ≈ $0.12/ft |
Power | 4 kW/hr @ 12 in/min = ~0.067 kWh = $0.01 |
Labor | 12 in/min = 1 ft/min = $0.67/ft |
Total per Foot |
TIG Welding Cost Example
Consumable & Indirect Costs:
Item | Cost Estimate |
---|---|
Filler (ER308L rod) | $12/lb; ~0.045 lb/ft = $0.54/ft |
Argon (pure) | $1.10/CFH @ 20 CFH = $0.18/ft |
Power | 5 kW/hr @ 6 in/min = ~0.167 kWh = $0.02 |
Labor | 6 in/min = 2 min/ft = **$1.34/ |
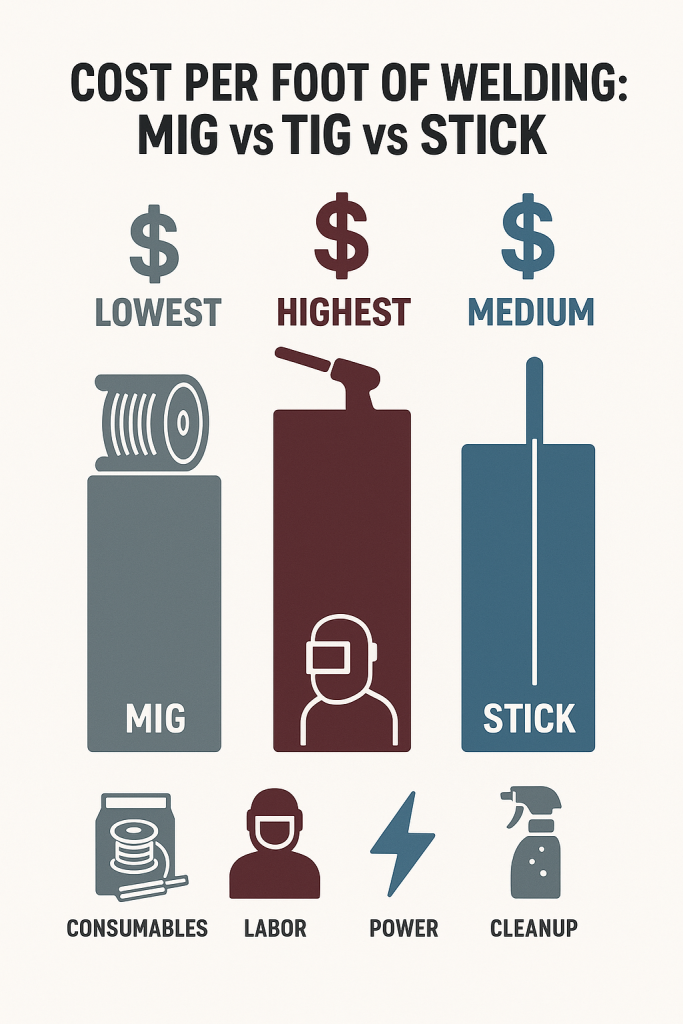